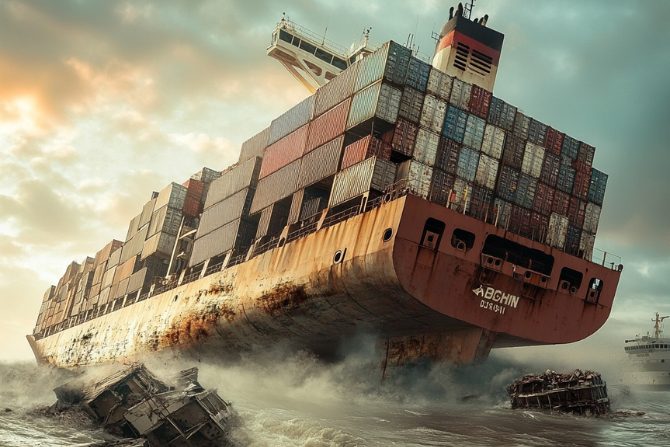
Every business aspires to operate smoothly, but unexpected supply chain disruptions pose a significant risk to the stability and success of the organization. In today’s hyper-connected marketplace, supply chain resilience isn’t just another industry term—it’s a critical component of business continuity and operational efficiency. The statistics are telling; that companies with resilient supply chains can boost their average ROI by up to 3-5% as per the latest industry studies. A fundamental shift in business approaches is underway as the traditional concern with low costs and optimization is being replaced with a focus on risk resilience. This suggests that supply chain resilience is no longer an option but an absolute necessity in a business environment where disruptions are the new normal. In this article, we’ll guide you through the essential steps and strategies to transform the goal of resilient supply chains into a solid, actionable plan to help you navigate risks and challenges with success.
Table of Contents:
- Understanding Supply Chain Resilience
- Strategies for Building a Resilient Supply Chain
- Reshoring or nearshoring: Think local
- Supplier diversification and risk assessment: Put your eggs in different baskets
- Data-based decision-making: Anticipate market behavior
- Creating inventory buffers: From just in time to just in case
- Enhancing supply chain visibility: See the full picture
- Risk management tools: Anticipate risks
- Measuring and Improving Supply Chain Resilience
- Collaborating for Supply Chain Resilience
- Leveraging Technology for Supply Chain Resilience
- FAQs in Relation to Supply Chain Resilience
- Conclusion
Understanding Supply Chain Resilience
Supply chain resilience has become a popular concept in the business world, and for good reasons. In a post-Covid world where disruptions have become a glaring reality, having a resilient supply chain is increasingly recognized as non-negotiable. The supply chain crisis effect that we witnessed in the wake of the pandemic showed how a single interruption can have a spiral-down effect on supply chain logistics, suppliers, and workforces on a global scale. Resilience is not simply about resisting threats or a fast recovery. A resilient supply chain is agile in the true sense; it is embedded in proven processes and cutting-edge technologies that enable it to forecast and anticipate risks and opportunities that the future may bring and respond in the most effective way. Business operations are forever exposed to external threats in the form of global disasters such as the recent pandemic, volatile markets, or rapid shifts in consumer behavior. But what exactly is supply chain resilience? Simply put, it refers to a characteristic of supply chains that gives them the unique ability to stand firm in the face of disruptions while enduring minimal impact on your business.
Why supply chain resilience is so important
The covid -19 was an eye-opening event that demonstrated how the interdependent nature of supply chains carries enormous potential for disruption. Imagine a scenario where a natural disaster strikes and suppliers fail to deliver the promised goods or worse still a cyber-attack unravels the transportation network. This can trigger a massive upheaval in your supply chain network and lead to negative consequences for your revenue, costs, and finally reputation. That’s where supply chain resilience comes into play. It acts as a secret weapon whenever the tide turns or things go beyond your expectations. According to a study by the Business Continuity Institute, around 75% of organizations fell victim to at least one event of supply chain disruption with each incident incurring a cost of a staggering $1 million The growing importance of supply chain resilience can be gauged from the fact that over 60% of supply chain leaders recognize resilience as a top priority against speed and efficiency.
Main supply chain challenges and risks
Businesses face a wide range of risks and challenges in the domain of supply chains that include geopolitical issues, labor shortages, and economic factors among others. While it is difficult to pin them all down, the following are the most critical risks that confront organizations.
1. Demand volatility: Customer demand fluctuates like a river’s ebb and flow, REA—like during Christmas, for instance—it can lead to stockouts or excess inventory.
2. Supplier disruptions: Any disruption on the supplier’s side such as a natural disaster or labor strike can impact the availability of raw materials and components.
3. Transportation disruptions: Delays or interruptions in transportation networks, like port congestion or road closures, can affect the timely delivery of goods.
To mitigate these risks, organizations need to develop robust risk management strategies and build resilience in their supply chains. This would make it easier to alleviate risks and minimize the impact of adverse events, along with an enhanced preparedness for future eventualities

Supply chains face challenges like demand fluctuations, supplier disruptions, and transportation delays, requiring strong risk management strategies.
Strategies for Building a Resilient Supply Chain
Now that we are clear about what makes resilience so critical for modern business, the question now arises what does it take to build a resilient supply chain? Truth be told, there is no one-size-fits-all approach or an all-encompassing theory that can work for all, but there are certain strategies that have endured the test of time for delivering concrete results.
Shift to local production centers
Notwithstanding the cost benefits of offshore production, they are a foremost risk factor Therefore, a primary strategy is to bring production closer to key markets, either by relocating manufacturing operations to your country (reshoring) or a nearby country (nearshoring). By minimizing the distance and lead times involved in the transportation of goods and services, nearshoring can drastically reduce the risks of depending on far-off supply chains. Reshoring and nearshoring can also improve responsiveness to changes in customer demand whilst lowering vulnerabilities to global market conditions.
Supplier diversification and risk assessment: Put your eggs in different baskets
The old saying, “Don’t put all your eggs in one basket.” Is highly relevant in the context of supply chains. Relying on a single supplier can be counter-productive in the long run. credible strategy is to diversify your supplier base or expand your supplier network By sourcing materials and components from multiple suppliers, you can reduce the risk of disruptions.
Instead of concentrating on a single supplier or region, a multi-sourcing strategy that relies on suppliers dispersed in different regions across the world, can actually help to distribute risks and ensure you don’t fall short of meeting the expectations of your customers. From a business point of view, it’s a smart move and one that can yield dividends in the long term. It needs to be realized that supply chain diversity is not just about having multiple suppliers. There is a proviso attached; each supplier comes with its own set of risks so you have to be mindful of that and access them beforehand. Risk assessment is an ongoing process that entails evaluating their financial stability, operational capabilities, and compliance with regulations and standards on a regular basis
Creating inventory buffers: From just in time to just in case
Conventionally, Just-in-time inventory management has been the norm for many companies. However, the growing unpredictability in the contemporary business environment has led to a paradigm shift towards a “just-in-case” approach. There is no such thing as a perfect inventory and therefore inventory planning aims at maintaining safety stocks just in case to cushion the impact of any supply chain shocks. Whether there is an abrupt spike in demand or a supply shortage, an inventory buffer helps your stock levels stay up to date without incurring the risk of excessive costs due to overstocking.

Switching from just-in-time to just-in-case inventory management ensures smoother operations during supply chain disruptions, but requires careful planning and real-time visibility
Risk management tools: Anticipate risks
The inevitability of risk reinforces the value of thorough risk management in any supply chain program. A variety of tools are used for this purpose that help to identify, assess, and eventually mitigate supply chain risks. The most widely used tools in this regard include high-risk assessment frameworks, scenario planning, and simulation modeling.
Risk assessment frameworks provide a structured approach to identifying and prioritizing risks based on their likelihood and potential impact. Scenario planning is a key tactic that involves playing out potential situations that might hamper supply chain processes and devising backup plans to minimize their impact. Simulation modeling utilizes computer models to simulate the behavior of the supply chain under different disruption scenarios like supplier issues or economic crises. Identify potential bottlenecks and vulnerabilities. With these tools in your toolkit, detecting potential hurdles early on before they escalate and coming up with strategic ways to steer clear of them is crucial for supply chain resilience.
Measuring and Improving Supply Chain Resilience
As the frequency and intensity of disruptions increase, it is critical to assess how resilient your supply chain is and whether it has the requisite capabilities to recover from any disruptive setbacks. There are several key metrics you can use to evaluate your supply chain’s resilience:
1. Time to recover: How long does it take for your supply chain to return to normal operations after a disruption?
2. Customer service level: Can you maintain customer service levels during and after a disruption? Gather customer feedback to see whether you can fulfill customer demands without fail
3. Inventory levels: Is your inventory well-equipped to keep up with varying customer demands in the face of a disruption?
4. Supplier performance: How well do your suppliers maintain delivery and quality performance during a disruption? Can the suppliers be trusted to deliver orders on time?
5. Financial impact: What is the financial impact of a disruption on your organization, including lost sales, increased costs, and damage to reputation?
By tracking these metrics, you can assess your current level of resilience and identify areas for improvement. You can also benchmark your performance against industry peers and best practices.
Time-To-Survive
Time-to-survive (TTS) is a metric that measures the maximum duration that it takes for a supply chain to align supply with demand following disruption. It’s like a countdown clock for your supply chain’s survival.
TTS is calculated by dividing the available inventory by the average daily demand. The higher the magnitude of TTS, the more resilient your supply chain is, as it has more time at hand to recover from disruptions without impacting customers.
You can improve your TTS by increasing inventory levels, diversifying your supplier base, and improving your supply chain visibility and agility. At the heart of it, you’re just giving yourself extra wiggle room to make a strong comeback.
Time-to-Recover
Time-to-recover (TTR) is another important metric that measures the time it takes for a supply chain to resume normal operations after a disruption TTR is influenced by various factors such as the severity of the disruption, the availability of alternative suppliers, and the effectiveness of your crisis management and business continuity plans.
The TTR can be improved by developing robust contingency plans, enhancing your supply chain flexibility and agility, and investing in technologies that enable rapid response and recovery. It’s all about getting back on your feet as quickly as possible. Another factor that can influence TTR is lead times as longer lead times in procuring necessary materials can hinder quick recovery. This suggests that even with robust contingency plans, prolonged lead times can extend the TTR which can have implications for supply chain resilience.
By reviewing these performance indicators, one can assess your current level of resilience and identify both weaknesses and areas for improvement in your supply chain strategy. An iterative approach to supply chains helps you continuously improve so that you don’t just survive but thrive in challenging times. You can also benchmark your performance against industry peers and best practices.

Measuring supply chain resilience involves key metrics like recovery time, customer service levels, and supplier performance to assess how well it can handle disruptions.
Digitize the way you Work
Digitizing your supply chain operations can significantly improve resilience by enabling real-time visibility, agility, and collaboration. It’s like giving your supply chain a digital upgrade.
Technologies such as the Internet of Things (IoT), artificial intelligence (AI), and blockchain can help you track and trace goods across the supply chain, predict and mitigate disruptions, and automate decision-making processes.
For example, IoT sensors can provide real-time data on the location and condition of goods, enabling you to quickly identify and respond to disruptions. Smart AI tools dive into supply chain info, getting ahead of what customers will want next and making sure stores have just the right amount of stock.
By digitizing your supply chain operations, you can improve your ability to anticipate and respond to disruptions, as well as optimize your overall supply chain performance. It’s like having a digital crystal ball for your supply chain.
Ecosystem Partnerships
Ecosystem partnerships involve collaborative relationships between various stakeholders within a specific ecosystem including suppliers, customers, logistics providers, and technology vendors, to achieve shared goals and create value in supply chains.
By working together, ecosystem partners can share information, resources, and expertise to identify and mitigate risks, as well as develop innovative solutions to supply chain challenges.
Ecosystem partnerships can take various forms, such as joint ventures, strategic alliances, and collaborative innovation networks. An example of this is when businesses work in tandem with their suppliers to develop contingency plans for tackling any unforeseen disruptions or cooperate with logistics providers to optimize transportation routes and modes.
Ecosystem partnerships provide an opportunity to capitalize on the strengths and resources of your ecosystem partners to drive innovation and enhance resilience in a complex and interconnected environment. Resilient and adaptive supply chain. A successful partnership is like having a supply chain dream team where your interests and business goals are taken care of.
Collaborating for Supply Chain Resilience
Here are some key tools and strategies that can foster collaboration between suppliers and their partners to achieve supply chain resilience.
Domestic policy tools can play a critical role in building supply chain resilience by creating a supportive environment for businesses that ensures operational continuity and nurturing partnerships between various stakeholders within a country.
Some key policy tools include:
1. Infrastructure investment: Investing in transportation, communication, and energy infrastructure can improve the efficiency and reliability of the supply chain.
2. Regulatory reforms: Streamlining regulations and reducing bureaucratic barriers can promote ease of business and enhance adaptiveness to changing conditions.
3. Tax incentives: Providing tax incentives for businesses that invest in resilience measures, such as inventory buffers or supplier diversification, can encourage the adoption of best practices.
By using these policy tools, governments can create a more resilient and supportive environment for businesses, reducing their exposure to supply chain disruptions.

Building a resilient supply chain requires collaboration and the use of policy tools like infrastructure investment, regulatory reforms, and tax incentives.
Public-private tools: Build trust
When members from both the public and private sectors join hands, this sets the stage for a strategic partnership based on trust and collaborative efforts that are beneficial for players in the supply chain.
These partnerships involve collaboration between government agencies and private sector organizations to address supply chain challenges, pool resources to upgrade infrastructure and regulate risks.
Some examples of public-private partnerships include:
1. Information sharing: Establishing secure platforms for sharing supply chain data and intelligence among government agencies and private sector organizations can improve visibility and enable early detection of disruptions.
2. Joint planning and exercises: Conducting joint planning and exercises can help government agencies and private sector organizations develop and test contingency plans for supply chain disruptions.
3. Research and development: Collaborating on research and development projects can lead to the discovery of new technologies and best practices for improving supply chain resilience.
By engaging in public-private partnerships, government agencies and private sector organizations can work together to build a more resilient and secure supply chain.
International tools: Keep markets open
International tools and agreements can reduce trade barriers to promote open markets and strengthen supply chain resilience on a global scale.
Some key international tools include:
- Trade agreements: Negotiating trade agreements that reduce tariffs and other barriers to trade allows businesses to diversify their supply chains as well as facilitate the free flow of goods and services across borders.
- Harmonization of standards: Setting product and process standards across countries can reduce the complexity and costs of compliance by standardizing supply chain practices. This is beneficial for businesses operating in multiple markets.
- Mutual recognition agreements: Establishing mutual recognition agreements for inspections, testing, and certification can reduce duplicative efforts and make cross-border trade more efficient.
Adopting global tools enables countries to work towards the goal of open, free markets and put up a united front against disruptions that bolster supply chain resilience.
Leveraging Technology for Supply Chain Resilience
With rapid digitization taking over the business world, supply chains are no exception. Unarguably, moving towards digitized supply chains can significantly improve supply chain resilience by enabling real-time visibility, agility, and automation. Advanced technologies can have a revolutionary impact when designing supply chains that are optimized for higher performance, productivity, and efficiency. Integrating digital technologies can herald a digital transformation in supply chain operations that empowers organizations to anticipate and adapt to market demands while reducing any inefficiencies that can result in significant cost savings across the supply chain.
A number of key technologies and strategies have emerged that can boost supply chain resilience that fall under the category of Supply Chain 4.0 technologies, such as the Internet of Things (IoT), artificial intelligence (AI), blockchain, and robotics. Some examples of how these technologies can be applied include:
1. IoT sensors: Using IoT sensors can help organizations track and trace the location and condition of goods in real-time and thus quickly identify and respond to disruptions.
2. AI-powered analytics: Applying AI algorithms to supply chain data can help organizations predict demand, optimize inventory levels, and identify potential risks and opportunities. This can have a positive impact on forecasting possible trends in customer demands and reducing risks of over- or under-stocking.
3. Blockchain: Blockchain aids in maintaining secure and transparent records of supply chain transactions that improve trust and collaboration among supply chain partners.
By leveraging these Supply Chain 4.0 technologies, organizations can build a more resilient, agile, and efficient supply chain that is better adapted to changing conditions and withstands disruptions.
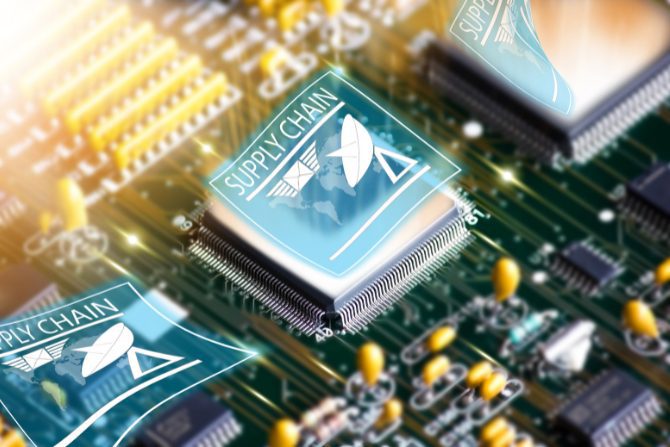
Technologies like IoT, AI, and blockchain are key to enhancing supply chain resilience by enabling real-time visibility and automation.
Achieving end-to-end visibility
End-to-end visibility is the holy grail of supply chain management. It means having a clear and comprehensive view of the supply chain in its entirety, from sourcing raw materials to delivery of finished products to customers.
Achieving end-to-end visibility requires a combination of technologies, such as IoT sensors, RFID tags, GPS tracking, data integration, and analytics.
By achieving end-to-end visibility, organizations can:
- Identify potential disruptions before they occur
- Optimize inventory levels and reduce waste
- Improve customer service and satisfaction
- Make data-driven decisions and adapt to changing conditions
Overall, visibility assists organizations to take advantage of faster response times and agility in supply chains and thus stay competitive in a dynamic business landscape
Implementing a supply chain control tower
A supply chain control tower works as a centralized command system that enables organizations to integrate data from multiple sources and enhance collaboration throughout the supply chain network. By facilitating informed and concerted decision-making, organizations are well-positioned to respond to disruptions quickly with minimum damage.
Implementing a supply chain control tower requires the integration of advanced technologies cloud computing, data analytics, and visualization tools—with processes and people.
Some key benefits of a supply chain control tower include:
- Monitoring what’s happening in the supply chain to get a clear perspective just got a whole lot clearer and more open, making it easier for everyone involved to stay informed.
- Faster response times to cope with disruptions and fluctuations in demand.
- Improved collaboration and communication among supply chain partners.
- Reduced costs and higher efficiency.
✐ Key Takeaway:
Boost your supply chain’s resilience by diversifying suppliers, leveraging data for decisions, creating inventory buffers, and improving visibility. Embrace tech like IoT and AI to predict disruptions and respond faster. Collaboration across the ecosystem is key to bouncing back from challenges.
FAQs in Relation to Supply Chain Resilience
What are the 4 pillars of supply chain resilience?
The four pillars are agility, flexibility, collaboration, and visibility. Together, they help businesses bounce back faster.
What are the five principles of supply chain resilience?
They’re diversification, integration, control (visibility), responsiveness (agility), and anticipation. This combo helps dodge disruptions.
What are the four keys to resilient supply chains?
The keys include robust design, redundancy in critical elements, flexibility to adapt quickly and a strong recovery strategy post-disruption.
How do we measure resilience in supply chains?
We gauge it by Time-To-Survive and Time-To-Recover metrics. They show how long a business can withstand disruption and recover.
Conclusion
To sum up, supply chain resilience isn’t about avoiding risks per se but rather about being well-prepared to address emerging issues and manage your supply chains in a way that maximizes efficiency and effectiveness. Deploying strategic moves like shifting towards local sourcing, collaborating with diverse suppliers across regions, and investing in data-driven predictive insights are all crucial steps toward building a robust and resilient supply chain that safeguards you against potential disruptions. As markets get more competitive over time, supply chain resilience can act as a source of competitive advantage for organizations so that they emerge stronger and faster whenever disruption strikes while catering to customer demands. Having a resilient supply chain not only makes it possible for organizations to respond swiftly and efficiently to any disruptive changes but also exploit opportunities in the current business environment to drive innovation and growth.